1. “Show locations on map” from a grid
In many locations in EIM, you can make a map directly from your query results. Click on the “folded map” icon on a results grid anywhere in EIM to open the GIS application, where you can then view and save your results as a map query layer.
So if you’re looking at TCE in specific locations, you can quickly map them and see what other parameters are present.
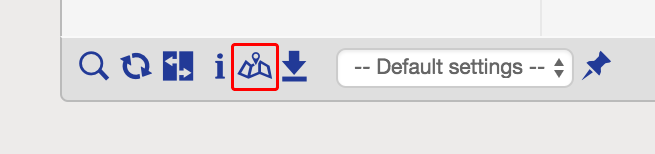
2. Save custom grid configurations
When you see a pushpin icon below a grid, that means you can name and save your current configuration in the grid, including column visibility, column order, sorting, and column width.
So if you use certain grids all the time, and prefer to view the data in a specific way, just click the pushpin and save your configuration for future use.
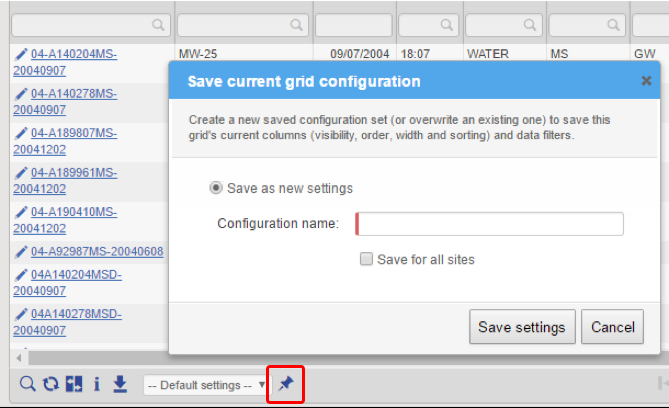
3. Save and share maps and reports on the dashboard
You can share saved maps and formatted reports with your colleagues and team members on the Project Manager Console dashboard. Saved maps and quick reports will show up under the sections “Quick Reports” and “Quick Maps”.
See Tip #4 to learn how to make this dashboard your default homepage.
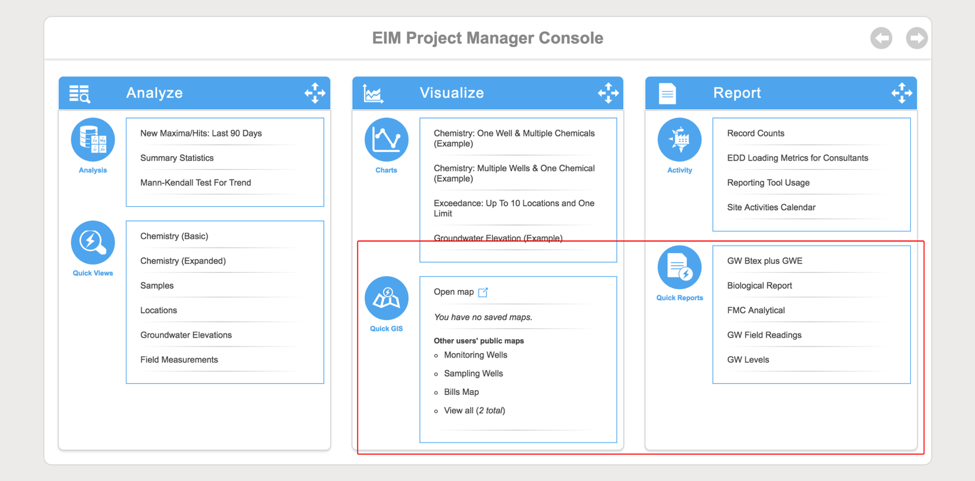
4. Set your homepage and your preferred default grid row count
EIM user options includes some very cool features. You can access your user options from the EIM menu: just click [your username] > Manage Profile.
Here, you can set your preferred homepage, enable filter options for easier login, and— our favorite— the option to adjust the default number of records to display in all EIM grids (20 is just never enough!)
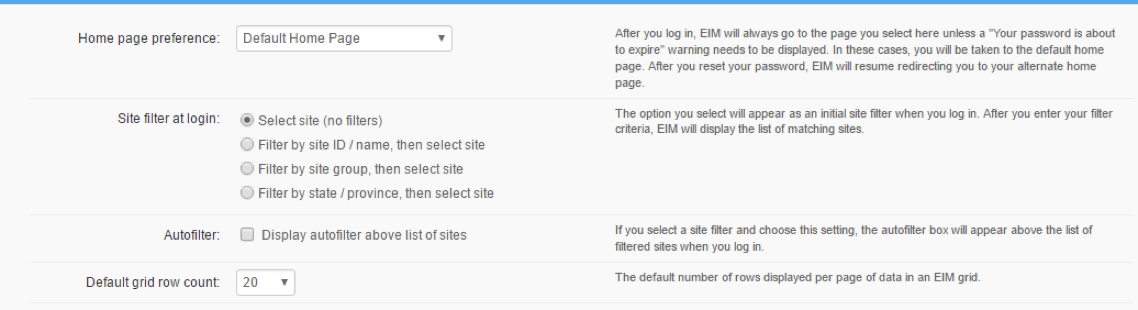
5. Lab Invoice Tracking
Full invoice tracking down to the parameter delivered level, to help you confirm that the lab gave you what you ordered, and that they’re charging you for exactly what they gave you.
You can find these forms at Input > Analytical > Lab Invoices.
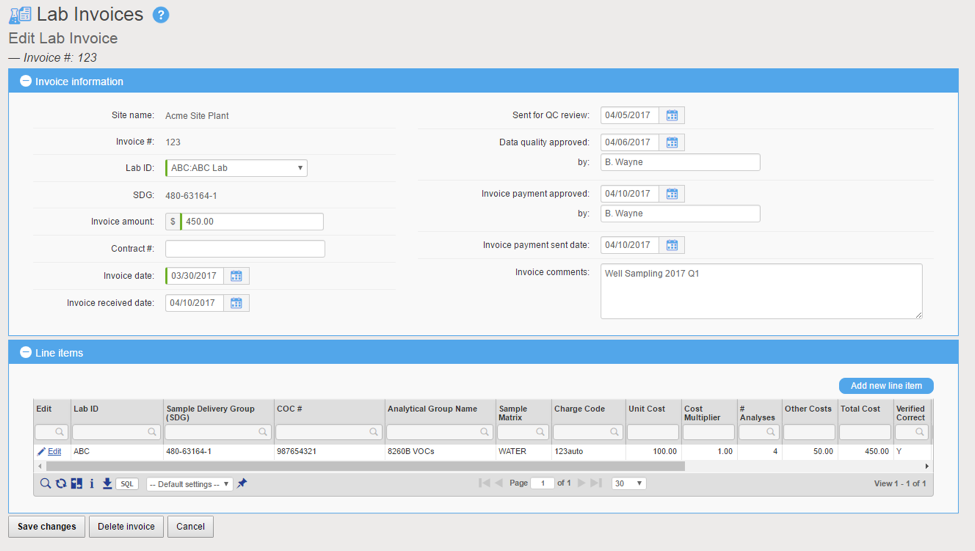
6. Simple or complex query building in a drag-and-drop interface
For users wanting to go beyond the standard “out-of-the-box” queries, EIM has an advanced query builder that lets SQL lovers go wild and share their results with other. You can even query data across multiple EIM sites to which you have access.
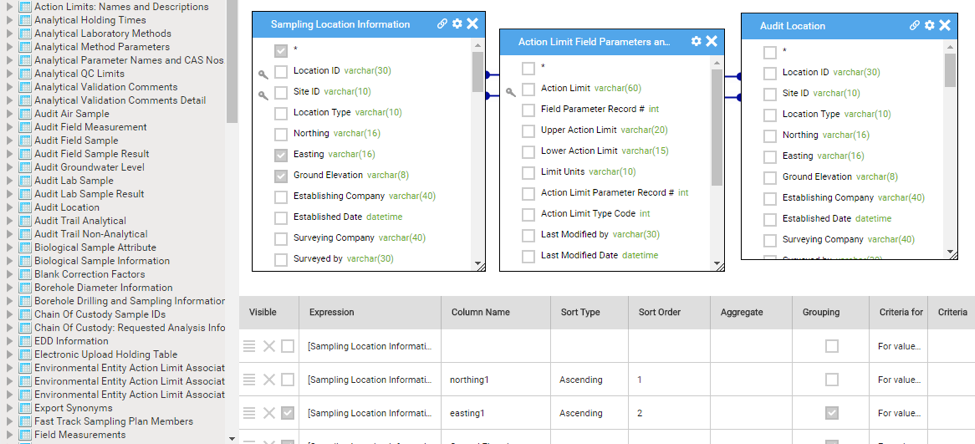
7. Easy data preparation for annual Consumer Confidence Reports (CCRs)
If you have the Locus EIM Water configuration, you will be able to prepare data tables for the CCR reports that all water providers are required to prepare annually. This is a huge timesaver compared to manually preparing these data summaries that are required by the Safe Drinking Water Act.
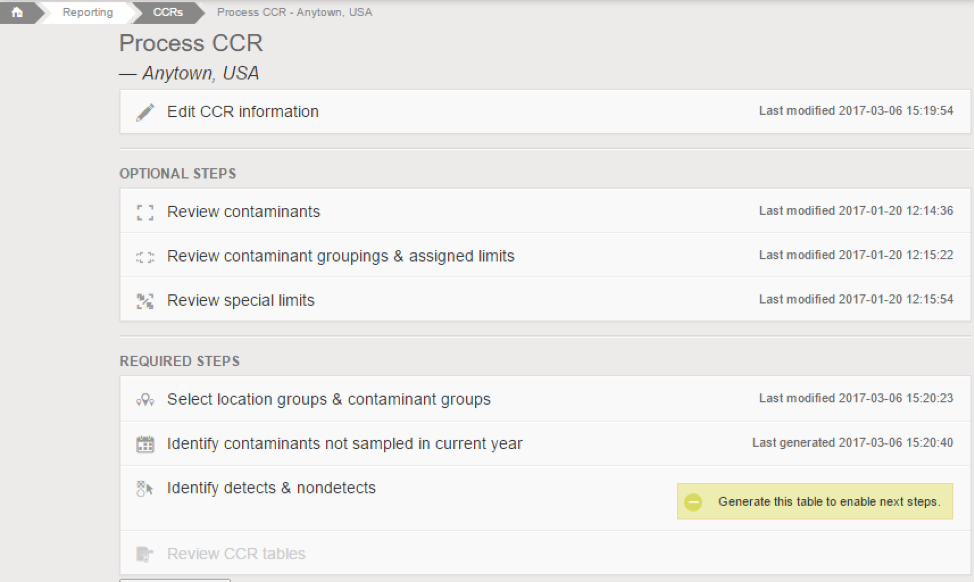
8. Send your sampling plan directly to your mobile device
With EIM’s integration with mobile, you can create a sampling plan in EIM and send that plan to one or more people to perform field sampling. This saves mountains of time and ensures your field teams have the correct information they need to collect their field data.
The sampling team can sync anytime to have team members back in the office review the interim data.
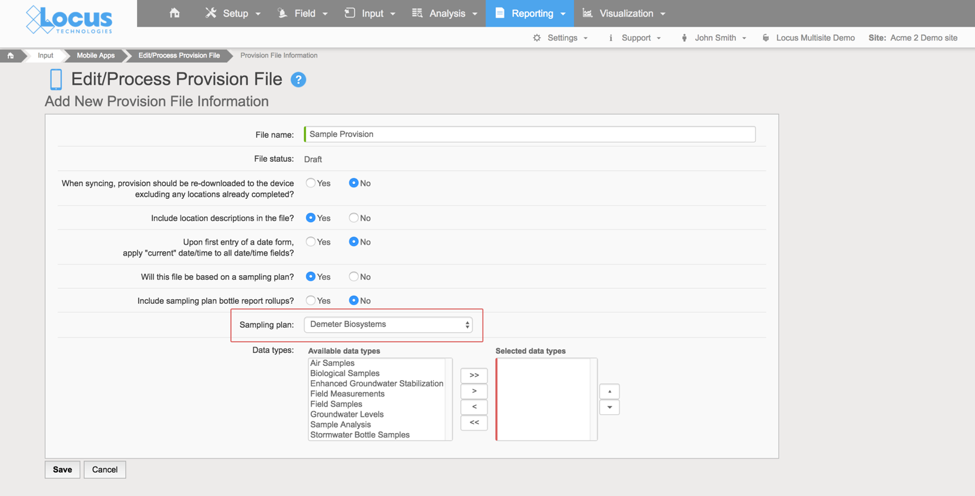
9. Create NetDMR submittals directly from EIM
If you have to submit EPA NPDES DMRs, EIM can create the electronic NetDMR output, saving you time and effort and banishing (hopefully) those old, complex, and overly difficult paper forms.
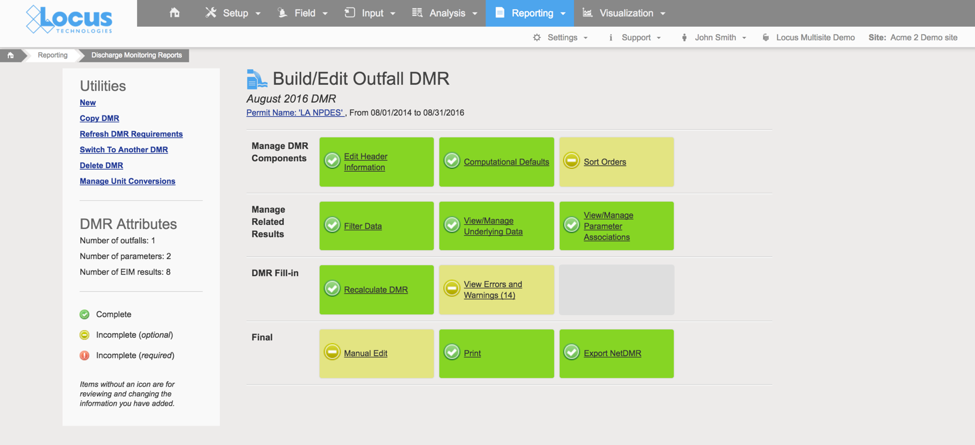
10. Support menu alerts you when new user guides, cheat sheets, training videos, or FAQs are posted
Locus is always busy creating new guide documents and help materials for our users, but it was hard to know when we added some new content. Now, our Support menu itself will flag you as soon as something new is posted so you can check it out!
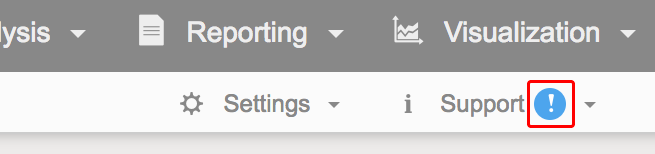